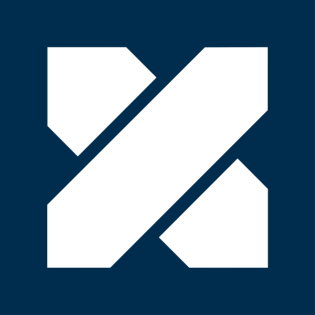
Prüfverfahren zur dynamischen Alterung von Werkstoffen
Im Gespräch: Prof. Uwe Franzke | Frau Dr. Franziska Krahl | Herr
Dr. Ulrich Zerweck-Trogisch
17 Minuten
Podcast
Podcaster
Beschreibung
vor 3 Jahren
Thema: Prüfverfahren zur dynamischen Alterung von
Werkstoffen
Im Gespräch: Prof. Uwe Franzke | Frau Dr. Franziska Krahl | Herr
Dr. Ulrich Zerweck-Trogisch
Prof. Franzke:
Herzlich Willkommen zur ersten Folge „Wissenschaft praktisch
erklärt“. Im Rahmen dieser Veranstaltungsreihe möchten wir
neueste Erkenntnisse und Erfahrungen aus Forschungsprojekten des
ILK Dresden vorstellen.
Heute sprechen wir über ein Prüfverfahren zur dynamischen
Alterung von Werkstoffen. Wir alle ärgern uns, wenn Produkte
schnell kaputt gehen und unsere Erwartungen an die Qualität nicht
erfüllt werden. Speziell die die zeitliche Änderung von
Werkzeugeigenschaften ist ein Problem, welches den Herstellern
große Schwierigkeiten bereitet. Dabei lassen sich viele
Erkenntnisse der Alterung im Vorfeld ermitteln, wenn man den
richtigen Partner mit dem richtigen Equipment an seiner Seite
hat.
Mein Name ist Uwe Franzke. Ich bin der Geschäftsführer des ILK
Dresden. Gemeinsam mit Herrn Dr. Ulrich Zerweck begrüße ich
unseren heutigen Gast, Frau Dr. Franziska Krahl ganz
herzlich.
Lassen Sie mich Frau Dr. Krahl kurz vorstellen. Sie hat an der TU
Dresden Chemie studiert und dort im Jahr 2008 promoviert. Seit
Juni 2012 ist sie wissenschaftlich-technische Mitarbeiterin am
ILK Dresden und arbeitet als Chemikerin u. a. auf den
Themengebieten Arbeitsstoffanalytik, Kältemittel- und Ölanalysen,
Alterungsuntersuchungen und Schadensanalysen. Herzlich
Willkommen.
Frau Dr. Krahl, wir werden heute über Ihr Forschungsthema
„Prüfverfahren zur dynamischen Alterung von Werkstoffen“
sprechen. Ganz ehrlich, das Thema klingt etwas sperrig. Daher
meine erste Frage: was genau muss man sich unter diesem Projekt
vorstellen?
Es geht in dem Projekt um Werkstoffe, um deren Alterung und um
ein Prüfverfahren, was die Alterung abbilden oder nachbilden
soll. Und der Kernpunkt ist die Art und Weise, wie die Werkstoffe
gealtert werden und zwar im Gegensatz zu existierenden Verfahren
altern wir die Werkstoffe in diesem Prüfverfahren auf eine
dynamische Art und Weise.
Prof. Franzke: Welche Werkstoffe muss man sich vorstellen? Unter
Werkstoffen kann man sich wie in unserem Fall in der Kältetechnik
Werkstoffe vorstellen, die Dichtungsmaterialen, Bauteil-relevante
Kunststoffe oder auch Schlauchmaterialien und im Einsatz müssen
diese Werkstoffe ihre Eigenschaft erfüllen, ihre Funktion
erfüllen und sind dabei Umgebungseinflüssen ausgesetzt. Wir haben
erhöhten Druck, erhöhte Temperaturen, wir haben das Kältemittel
und das Kältemaschinenöl und während des Einsatzes werden die
Werkstoffe beansprucht und dabei altern sie, sollen aber ihre
Eigenschaften erhalten und ihre Funktion möglichst lange
erfüllen. Und wenn man nun wissen möchte, ob ein Werkstoff in
einer Anlage eingesetzt werden kann, muss man diese prinzipielle
Eignung nachweisen und das macht man mittels standardisierter
Prüfverfahren, die die Alterung simulieren. Und das bezeichnen
wir auch als Beständigkeitsprüfung und in den existierenden
Verfahren werden die Werkstoffe dabei auf eine Art und Weise
gealtert, die man als statisch bezeichnen kann.
Dr. Zerweck: OK, statisch heißt, man beaufschlagt einfach mit
einer gewissen Belastung und was wäre jetzt der Unterschied zum
dynamischen Test?
Frau Dr. Krahl: ich würde das kurz erklären, vor allem wie die
statische Alterung abläuft üblicherweise. Man altert bzw. stresst
den Werkstoff, in dem man ihm den in der Anlage eingesetzten
Medien, wie Kältemittel und Kältemaschinenöl aussetzt und zwar
bei erhöhter Temperatur und Druck und dafür gibt man dem
Werkstoff zusammen mit dem Kältemittel und dem Kältemaschinenöl
in ein Druckgefäß und lagert dieses über eine bestimmte Zeit –
üblicherweise zwischen 3 und 10 Wochen – in einem Wärmeschrank
bei einer definierten Temperatur aus und die Temperatur ist dabei
im Vergleich zur Einsatztemperatur des Werkstoffes deutlich
erhöht, womit man einen zeitraffenden Effekt erzielt und damit
die Prüfzeit verkürzt. Vor der Auslagerung und nach der
Auslagerung bestimmt man die Eigenschaften des Werkstoffes,
Masse, Volumen, Härte, Zugeigenschaften und vergleicht die
miteinander und für die max. zulässigen Änderungen gibt es
Bewertungskriterien und die muss ein Werkstoff erfüllen. In der
Vorgehensweise, die ich gerade beschrieben habe, liegt der
Werkstoff während der gesamten Auslagerungszeit im
Kältemittel-Öl-Gemisch, also statisch. Das kann man zur
Veranschaulichung mit dem Einweichen eines schmutzigen
Wäschestücks vergleichen. Der Schmutz im Wäschestück soll ins
Wasser übergehen, wohingegen Dinge, die im Wäschestück enthalten
sein sollen, wie Farbe oder Aufdrucke natürlich verbleiben
sollen. Und wenn ich das Wäschestück einfach nur im Wasser
einweiche, also statisch drin liegen lasse, habe ich zunächst
einen sehr hohen Konzentrationsgradienten zwischen Schmutz im
Wäschestück und Schmutz im Wasser. Das heißt, zu Beginn löst sich
sehr viel Schmutz in dem Wasser und mit der Zeit sinkt aber diese
Konzentrationsdifferenz und es stellt sich ein sogenanntes
Lösungsgleichgewicht ein. Und wir alle wissen, dass durch quasi
reines Einweichen eines Wäschestücks im Wasser dieses nicht
vollständig sauber wird.
Dr. Zerweck: Und deshalb schließt sich dann anschließend die
dynamische Auswaschung, die dynamische Alterung des
Werkstückes/Werkstoffes an?
Frau Dr. Krahl: Genau. Wir haben das damit übertragen, also
übertragen auf den Auslagerungsversuch, der Werkstoff ist das
Wäschestück und das Kältemittel und das Kältemaschinenöl sind das
Wasser. Und unter dem Schmutz verstehen wir die Bestandteile, die
durch das Kältemittel und das Wasser aus dem Werkstoff
herausgelöst werden können, also die Komponenten, die eigentlich
nicht kompatibel mit dem System sind. Und das sind bei
Werkstoffen üblicherweise Weichmacher, Verarbeitungsadditive oder
sogar die Grundbausteine des Werkstoffes selbst. Da in den
existierenden Beständigkeitsprüfungen der Werkstoff nur
eingeweicht wird, wird auch sich dort ein
Löslichkeitsgleichgewicht einstellen und mit der Zeit sinkt der,
also der Konzentrationsgradient minimiert sich und irgendwann
geht von diesen löslichen Bestandteilen nichts mehr in das
Kältemittel oder Öl über, obwohl es das theoretisch noch könnte.
Und dieser Zustand ist nicht auf den Betrieb einer Kälteanlage
übertragbar. Denn in der Kälteanlage ändert das Kältemittel ja
immer wieder seinen Zustand zwischen flüssig und gasförmig. Und
wenn der Werkstoff z. B. in einer Kälteanlage immer wieder mit
dem flüssigen Kältemittel in Kontakt steht, kann man sich
vorstellen, dass sich dabei lösliche, nicht kompatible
Bestandteile aus dem Werkstoff lösen und durch das Kältemittel
mitgerissen werden. Wenn das Kältemittel dann in den gasförmigen
Zustand übergeht, dann werden diese gelösten Bestandteile nicht
mit in den gasförmigen Zustand übergehen üblicherweise, sondern
sie separieren sich vom Kältemittel und fallen im ungünstigsten
Zufall an irgend einer Stelle im Kreislauf aus und lagern sich
ab. Wenn das Kältemittel anschießend wieder verflüssigt wird,
enthält es diese gelösten Bestandteile nicht mehr und ich habe
wieder den max. Konzentrationsgradienten, wenn das Kältemittel
den Werkstoff wieder sieht. Genau dieser Effekt wird in den
statischen Beständigkeitsuntersuchungen nicht abgebildet, und
deswegen haben wir genau dieses Verfahren entwickelt.
Dr. Zerweck: Man wäscht also immer wieder mit neuem sauberem
Kältemittel aufs Neue, aufs Neue und aufs Neue aus.
Frau Dr. Krahl: Genau, so macht man das.
Prof. Franzke: Vielen Dank für die Erklärung. Klingt schon mal
sehr spannend. Aber was war die Motivation für dieses Vorhaben?
Sie wollten ganz sicher nicht verstehen, wie man Wäsche
wäscht.
Frau Dr. Krahl: Nein. Die größte Motivation war in der Tat die
Tatsache, dass wir etwas an den existierenden Verfahren
verbessern wollten mit der Abbildung des Phasenwechsels des
Kältemittels im Kältekreislauf. Das war unsere ursprüngliche
Intension, um dieses Löslichkeitsgleichgewicht zu vermeiden, denn
es gibt Fälle, wo Werkstoffe beständig geprüft werden aber in der
Praxis versagen, weil die Bedingungen dort eben doch auf das
Herauslösen von Komponenten harscher sind. Eine zweite Motivation
für dieses Projekt resultiert aus dem verstärkten Einsatz von
Kältemitteln mit geringem Erderwärmungspotenzial, wodurch sich
ein erhöhter Bedarf an der Vorhersagen der Langzeitstabilität von
Werkstoffen ergeben hat in den letzten Jahren. Wir alle wissen,
es gibt zahlreiche neue Kältemittel und vor allem auch zahlreiche
neue Kältemittelgemische und es gibt wenige bis gar keine
Verträglichkeits- bzw. Beständigkeitsdaten dafür und die
individuelle Prüfung ist langwierig, zeitaufwändig und da haben
wir nach einer Möglichkeit gesucht, dieses Prüfverfahren in einer
beschleunigten Art und Weise zu modifizieren. Dann gibt es noch
einen dritten Punkt: In den existierenden
Beständigkeitsuntersuchungen wird ja der Zeitraffer durch eine
erhöhte Temperatur ermöglicht, und man möchte immer am liebsten
eine lange Einsatzdauer in möglichst kurzer Prüfzeit abbilden.
Jetzt können wir uns aber alle vorstellen, dass man dafür die
Temperatur im Vergleich zum Einsatz deutlich überhöhen müsste,
was am Ende dazu führt, dass der Werkstoff schlicht durch
thermische Effekte zerstört wird. Häufig bleibt also nur eine
lange Prüfdauer. Und da schließt auch unser Prüfverfahren an,
verkürzte Prüfzeiten zu ermöglichen.
Dr. Zerweck: In Ordnung. Warum ist es nun wichtig, die
Alterungseffekte von Dichtungsmaterialien in Kältekreisläufen zu
verstehen und zu bewerten?
Frau Dr. Krahl: Einerseits führt der Eigenschaftsverlust von
Werkstoffen oder von Dichtmaterialien in Kälteanlagen zum Verlust
der Dichtheit und damit zum Verlust von Kältemittel, welches
einerseits in die Umwelt austritt und andererseits bricht die
Leistung in der Anlage ein. Hinzu kommt noch, dass das
Herauslösen von Additiven oder von Werkstoffbestandteilen aus
einem Werkstoff auch dazu führt, dass sich diese auch irgendwo im
Kreislauf ablagern und auch dadurch unerwünschte Effekte
auftreten. Und letztendlich, wenn man diese Alterungseffekte von
Werkstoffen gut versteht und auch gut geprüfte Werkstoffe
einsetzt, minimiert man Serviceeinsätze und Kosten und man
minimiert auch die Umweltbelastung.
Prof. Franzke: Wer genau ist der Adressat für Ihre Erkenntnisse?
Wer benötigt solche Informationen?
Frau Dr. Krahl: Ich denke da in erster Linie an Hersteller von
Werkstoffen, gerade die für neue Kältemittel oder auch für
Formulierungen Werkstoffe testen und qualifizieren müssen und
außerdem auch an Hersteller, Konstrukteure und Planer von
Kälteanlagen.
Prof. Franzke: Könnte man sich auch noch andere Anwender
vorstellen außerhalb des Kältetechnikbereiches?
Frau Dr. Krahl: Eindeutig ja. Im Grunde genommen kann man
letztendlich mit vielen Prüfmedien Werkstoffe untersuchen oder
auch Bauteile. Die Grundvoraussetzung für das Verfahren, was wir
anwenden, ist, dass das Prüfmedium einen Phasenwechsel zwischen
flüssig und gasförmig aufweist.
Dr. Zerweck: Welche Werkstoffe kann man mit Ihrem Verfahren
untersuchen und neue Erkenntnisse daraus gewinnen? Bei welchen
geht das Ganze nicht?
Frau Dr. Krahl: Nicht fallen mir auf Anhieb erst mal keine ein.
Ich kann mir da prinzipiell sehr viele vorstellen. Ich denke an
Metalle, an Verbundwerkstoffe, an Klebstoffe oder auch an
Klebverbindungen. Die Grundvoraussetzung meiner Meinung nach ist,
dass man an diesem Werkstoff auch eine Eigenschaft vorher und
hinterher prüfen kann.
Dr. Zerweck: Kunststoffe gehen genauso?
Frau Dr. Krahl: Genau, Kunststoffe gehen genauso. Das ist bei den
Werkstoffen schon mit dabei. Von daher sehe ich dort wenige
Grenzen an Materialien.
Prof. Franzke: Wo genau liegen die Herausforderungen vor allem
unter wissenschaftlicher Sicht? Wo waren die Schwierigkeiten bei
der Projektbearbeitung?
Frau Dr. Krahl: Die Schwierigkeiten in der Projektbearbeitung
waren, also wir hatten eine große Herausforderung, wollten neben
dem Kältemittel-Phasenwechsel auch den Umlauf des
Kältemaschinenöls im Kreislauf, den man ja nicht vermeiden kann,
mit abbilden. Das ist uns gelungen. Das war auch die größte
Herausforderung, aber auch unser größter Erfolg in dem Projekt,
dass uns das gelungen ist. Ich sehe als große Herausforderung,
dass es in Bezug auf dieses neue Prüfverfahren natürlich keine
Normung und keine wirklichen Vergleichswerte gibt. Wir konnten
bisher im Rahmen des Projektes nur für wenige Kältemittel und Öle
Werkstoffkombination die Korrelation herstellen zwischen der
dynamischen und statischen Alterung, aber eben nur für wenige und
da fehlen einfach nur Vergleichswerte.
Dr. Zerweck: Wo gibt es noch Probleme bei den Prüfverfahren?
Gibt’s Stellen, wo Sie sagen, das haben wir noch nicht im
Griff?
Frau Dr. Krahl: Nein. Ich finde, dass wir in dem Prüfverfahren
schon viel im Griff haben. Ich sage mal so, unsere klassischen,
diese statischen Beständigkeitsuntersuchungen sind so sehr
Routine, dass das wie von alleine durchläuft. Da sind wir bei dem
neuen Prüfverfahren immer noch, dass wir so eine Art
Anlaufprozess haben, je nach Kältemittel, je nach
Kältemaschinenöl, dass man da noch ein paar Einstellungsparameter
vorweg ermitteln muss. Aber ansonsten.
Dr. Zerweck: Und gewisse Stoffe, die man nicht herauswaschen
kann, die man nicht gelöst bekommt? Gibt es da irgendwelche
Beschränkungen, die Sie bisher gefunden haben?
Frau Dr. Krahl: Wenn ich einen Stoff nicht herausgelöst bekomme,
ist das an sich ja erst mal gut. Weil es ein Zeichen dafür ist,
dass er sich durch das Kältemittel oder das Kältemaschinenöl in
der Tat nicht herauslösen lässt und das ist für die Beständigkeit
des Werkstoffes eigentlich erst mal positiv.
Prof. Franzke: Jetzt habe ich mir Ihren Versuchsaufbau ja mal
angeschaut und Sie verwenden ja eine Art Geysir, um also dort
diese permanente Konzentrationsgefälle aufrechterhalten zu
können. Als Chemikerin eher ungewöhnlich, dass Sie Geysire
konstruieren und bauen oder gab es dort eine
Zusammenarbeit?
Frau Dr. Krahl: Ich gebe zu, in diesem Projekt gab es eine ganz
großartige Zusammenarbeit gerade mit unseren Konstrukteuren,
technischen Mitarbeitern und auch unseren Werkstoffspezialisten,
welche ich ja auch nicht von Haus aus bin. Ich hatte da große
Unterstützung, dass da sich da viele Leute konstruktiv Ansätze
überlegt haben, wie wir dieses innovative Konzept des Ölumlaufes
dort integrieren können.
Prof. Franzke: Wenn man das Projekt sich mal anschaut, gibt es
etwas, wo Sie sagen, da müssen wir weitermachen, da ist noch
Erkenntnisbedarf?
Frau Dr. Krahl: Ich möchte vielleicht am liebsten eine besondere
Stärke des Verfahrens betonen. Was sich dann, das schließt sich
daran an, dass da vielleicht noch ein bisschen Ausbaubedarf ist.
Aber die Stärke des Verfahrens liegt ja einerseits in der
Anwendungsnähe zum Kältekreislauf. Aber eine wirkliche große
Stärke ist die deutlich kürzere Prüfdauer bei einer deutlich
niedrigeren Prüftemperatur. Wir haben im Rahmen des Projektes für
ausgewählte Werkstoffe ja vergleichend statisch und dynamisch
geprüft und festgestellt, dass wir mit unserem dynamischen
Prüfverfahren 5-fach schneller den Werkstoff altern und das bei
bis zu 60 K geringerer Prüftemperatur. Um ein Gefühl dafür zu
bekommen bei einem 2-wöchigen statischen Auslagerungstest bei 130
° erzielt man dasselbe Ergebnis mit dem dynamischen Prüfverfahren
über 2 Tage bei 70 °und das bietet natürlich gerade in Bezug auf
Screening-Untersuchungen oder so immense Vorteile. Und da ist
jetzt unsere Aufgabe, das jetzt soweit nach außen zu tragen, dass
man das auch wirklich versteht, wie effektiv dieses neue
Prüfverfahren im Vergleich zu den existierenden Methoden
ist.
Dr. Zerweck: Was einmal den Einsatz der Werkstoffe viel näher und
praktischer ansetzt und einsetzt als es durch so ein statisches
Prüfverfahren bei erhöhter Temperatur 130 °C irgendwie abbilden
würde.
Frau Dr. Krahl: Genau. Es gibt ja schlicht Werkstoffe, die sehen
diese 130 ° oder selbst vielleicht 120 ° in der Realität nie,
aber sie müssen ja geprüft werden und ich kann nicht ein Jahr
lang einen Werkstoff prüfen. Dafür hat kein Hersteller Zeit. Das
kann ich jetzt mit dem Verfahren eben auch bei quasi
Einsatztemperatur oder nur bei leicht erhöhter
Einsatztemperatur.
Dr. Zerweck: Haben Sie noch weitere wissenschaftliche
Herausforderungen, die noch warten, wenn Sie die Palette
vielleicht noch mal erweitern wollen weg von nur Kältekreislauf
und das Ganze verallgemeinern?
Frau Dr. Krahl: Ich gebe zu, ich bin ja auch für Vorschläge
offen, wir selber haben eher den Anspruch, dass wir das als
Routinemethode etablieren wollen. Aber ich kann mir vorstellen,
dass wir auch in andere Richtungen gerne
weiterentwickeln.
Dr. Zerweck: Routinemethode vornehmlich erst mal für Kältemittel
und Kältekreislauf, Anlagen und Komponenten.
Frau Dr. Krahl: Genau
Prof. Franzke: Ich habe mal versucht, Ihre Ideen zusammenzufassen
und die Frage, die ich Ihnen gerne stellen würde, ob Sie meiner
Zusammenfassung folgen können. Umweltschutz und
Funktionssicherheit von Kälteanlagen können mit Hilfe der
vorgestellten Untersuchungsmethode auch bei neuen
Dichtungsmaterialien und neuen Kältemitteln bzw. Kältemittelölen
sichergestellt werden.
Frau Dr. Krahl: Da stimme ich Ihnen voll und ganz zu.
Prof. Franzke: Dann ganz herzlichen Dank für das tolle Gespräch
und ich wünsche Ihnen allen weiterhin viel Erfolg bei der
Projektbearbeitung. Danke.
Frau Dr. Krahl: Ganz vielen Dank
Weitere Episoden

18 Minuten
vor 1 Jahr

24 Minuten
vor 1 Jahr

16 Minuten
vor 2 Jahren

18 Minuten
vor 2 Jahren
Kommentare (0)